5Sは現場改善の基本
5Sとは整理・整頓・清掃・清潔・躾(「習慣」という場合もある)のことをいいます。生産(作業)現場を持っている会社にとっては、一度は取り組んだことのある方も多いと思います。
5Sの言葉だけからイメージすると、容易な活動に思えるかも知れませんが、生産性向上のために本気でやろうとすれば、社運をかけた一大プロジェクトとも言えるくらいのものなのです。目先だけや一時しのぎの5Sでは、一時的に物が片づき綺麗になっただけで満足してしまいます。しかし、時間が経てばすぐに元の乱雑で汚い現場に戻ってしまい、生産性の改善も進みません。
筆者も製造業の現場改善を支援するとき、多くの場合に5Sが取り組みテーマとなります。しかし、いつも良い結果が得られるわけではありません。
今回は、その中でも成功事例の一つといえるD社での取り組みを紹介します。D社では極めて短期間のうちに5Sを相当レベルまで実施し、大きな生産性向上につなげることができました。5Sを成功できる会社は何が違うのでしょうか?
D社での5S活動
D社は、社員12名で産業機械の板金加工から組立などを受託する企業です。自動車生産工場向けなどの比較的大型機械が多く、500屬曚匹旅場には組立作業のスペースを確保しながら、板金加工機械などが据え付けられています。
基本的に受託機械製品は、たくさんの構成部品で成り立っており、また受注する製品はそれぞれ種類が異なっています。そのため、入荷した部品が散乱したり、作業段取りが円滑に行えないことが日頃の悩みでした。また使用する工具類なども個人によって管理がまちまちで、故障や紛失したりして、作業の進行に支障をきたすこともありました。
そのような中で、ちょうど2008年後半からは世界不況のあおりを受け、D社でも生産が激減しました。仕事がないなら、この機会に生産性向上の改善に取り組もうとしたことがキッカケです。
まずD社では、全社員が集まり5Sのビデオを視聴したり、教材をもとに基本的な5Sの取り組み方法を学びました。そして社員が一丸となって取り組んだことで、数ヶ月で見違えるほど現場が変わったのです。
成功のポイント
短期間で極めて高いレベルの5Sを実現できたことの理由はいくつかありますが,おおよそ以下の3つに集約することができます。
|
(1)工場長の率先垂範 |
|
5S教育での手順をもとに、工場長自らが実践をしました。特に最初の「整理」の段階においては、しばらく使っていない物を不要物とするには思い切りが必要です。5Sで最初につまずきやすいのは、不要物の処分について責任の所在が不明確になることです。ここではトップが勇気を持って、自らの責任下において撤去・処分を判断し指示しました。 |
|
(2)改善の道具を作る器用さ |
|
必要なものを必要なところに備えておく「整頓」においては、整頓を行うための棚やラックなどの道具が必要です。しかし、一般的な市販品だけ使っていては、実用的な整頓ができない場合もあります。だからと言って、整理棚などの特注品を作るようでは、とても費用がかかってしまいます。D社は金属加工を本業であるため、必要な整理棚は自分達で考案して作成しました。 |
|
(3)使い終わった後の清掃の徹底 |
|
5Sの最後の「躾」ができなければ、それまでの3S(整理、整頓、清掃)がどんなにできても、職場を清潔に保つことはできません。特に注意しなければならない領域は、複数の人が共同で使う機械や作業場です。D社においては、使用した後には必ずもとの清潔状態に戻すことを一人一人が徹底しました。
公共施設などの掲示で見かける「来たときよりも美しく」の実践です。 |
実際の改善例
ここで紹介している改善事例の道具は、すべてD社で製作したものです。この実績と加工業の経験をもとに、今後は他社からも要請があれば、専用の改善道具製作の受託もしたいと考えています。
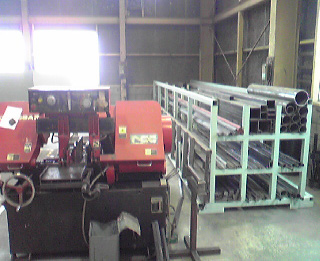 |
<棒状端材の整理棚>
切断機の横に設置して余った材料をムダなく使用できる |
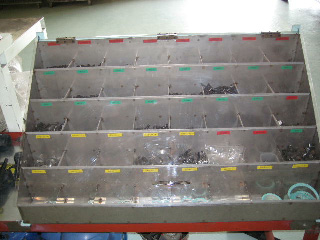 |
<ネジ・小物類の種類別の収納箱>
適当な段差デザインと透明のカバーによって、視認性を確保している |
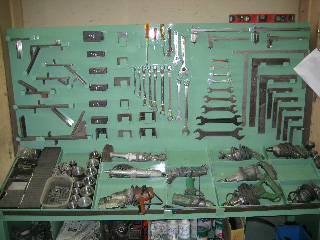 |
<工具類の立て掛けタイプ収納ボード>
それぞれの工具の形状に合わせた保持方法を考案 |
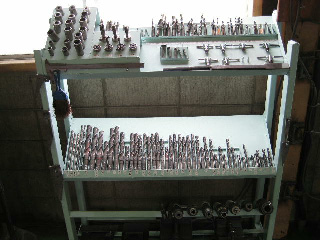 |
<ドリルの収納棚>
ドリルのサイズに合わせた配置方法を工夫し捜す手間がなくなった |
5S展開のポイント
5Sを展開する場合の進め方として、5Sを「改善活動」と「維持活動」に分けて行うと、成功の確率が比較的高くなります。
改善活動とは、「整理」と「整頓」です。整理とは、D社の工場長が行ったように「不要なもの」と「必要なもの」に仕分けすることです。整頓とは、必要なものを「適量」を「定位置」を決め「分かりやすく収納」することです。つまり、作業環境を最善の状態にすることです。
最善とは、
・歩数を少なくする
・手数を少なくする
・探さない
の3つの要件を満たすことです。D社の事例でいえば「ネジ・小物類の種類別収納箱」や「工具類の立て掛けタイプ収納ボード」「ドリルの収納棚」などがそれに当たります。
【改善活動の2S 】
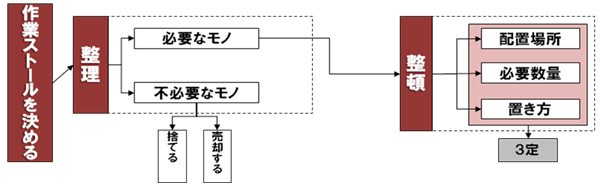
作業環境が最善の状態になったら、この状態を維持する活動が「清掃」「清潔」「躾」の3Sです。日々においては、この3Sの繰り返しになります。3Sでは、躾の「原価意識の向上」を全社員がどれだけ共有できるかがポイントになります。汚すことのムダ、乱れた状態にすることのムダなどを徹底して教育することが重要です。D社が素晴らしいのはドリル周囲に切りくず一つ落ちていない状態がキープできていることです。
【維持活動の3S 】
いまさら「5S」などとタカをくくっていないで、改めて挑戦してみてください。その際に、5Sは「綺麗にするため」に行うのではなく「生産性向上=コストダウン」のために行うという目的をぶれさせないことです。
|