今回は、パネル交換・溶接作業時の一つの「クォーターパネル」交換する場合、カット位置を変更することにより作業効率アップについて書かせていただきます。
最近の車の中でも、特に乗用車や軽自動車のFrピラーからロッカーパネル、センターピラー、ルーフサイドレール、クォーターパネルまで一体の一枚鋼板の車両が増えています。おそらく、製造工程の簡素化や、きしみ音の防止などの理由だと思われます。 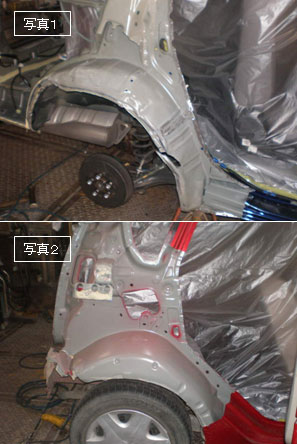
そのためにワンボックス車や、少し前の乗用車のように、クォーターパネルのロア部、ロッカーパネル接合部に基準の位置がありません。したがってパネル下の作業がやりにくい位置でカット作業(写真1)を、行わなければいけなくなりました。メーカーの修理マニュアルを見ると、カット位置はパネル下で作業をするように指示してあります。メーカーは、実作業の容易性などを考慮して、マニュアルを作成してほしいものです。これが、この業界のダメな部分であると思いませんか?
そこで、わが社では、このカット位置をずいぶん前から変更することで、作業性を改善しています。カット位置としては、破損状況にもよりますが、タイヤハウスの細い部分(写真2)でパネルカット作業し、溶接は歪が干渉しにくい部分を溶接するようにしました。
理由をあげてみます。
- 下向きの作業を行わなくてすみ、重要な溶接点やラインがあり、位置取りがしやすい
- Cピラーのような太い部分でなく、溶接が用意である
- 溶接部分の幅が比較的に短く、歪みにくい
- 強度的にあまり重要な部分でないので、指示書通りの作業でなくてもむ問題が少ない
- タイヤハウスでの溶接により、位置取りのミスがなくなり、ドアとの隙間違いなどのミスが無くなる
- 3と似たような内容になるが、仕上げのパテ作業も作業しやすい。
以上な部分が簡素化できます。
今までのような作業を行わなければならない時も当然ありますが、9割がた上記のような作業で行えています。当然ミスも無くなり、作業者も楽に作業しています。
通常であれば見積金額は、作業時間に換算して指数を設定していますよね。ですから、指数で10の場合は、10の金額しか請求できませんが、その分作業を早く行うことで、利益とコストダウンに直結させて行くのが経営だと思います。
少しの工夫でカット作業や溶接作業が容易になり、さらには納期が早くなるためにお客様満足度も高まります。そして、利益やコストダウンが図れる作業要領を常に考えていきましょう。
|